Revitalize Your Turbines: Top Refurbishment Techniques

Turbines are the backbone of many industries, from power generation to aerospace and manufacturing. Over time, wear and tear can reduce their efficiency, leading to higher operational costs and potential failures. Rather than investing in expensive replacements, refurbishment offers a cost-effective solution to extend turbine lifespan, enhance performance, and maintain reliability. In this blog, we’ll explore the top refurbishment techniques that can breathe new life into your turbines. From advanced coating applications to precision machining and blade reconditioning, these strategies will help you maximize efficiency while minimizing downtime.
In this guide, we will explore effective turbine refurbishment techniques designed to enhance the performance and extend the lifespan of gas and steam turbines. Topics include advanced blade repair methods, strategies for extending component life, minimizing operational costs, utilizing advanced materials and design improvements, and managing turbine component fatigue.
Signs Your Turbine Needs Refurbishment
Turbines play a critical role in many industrial and energy systems, but like any high-performance machinery, they don’t last forever. Over time, wear and tear can compromise their efficiency, performance, and safety. Identifying when your turbine needs refurbishment is crucial to preventing costly downtime and ensuring continued optimal performance.
There are several signs that indicate it might be time to consider refurbishment for your turbine. These include unexplained vibrations, a drop in efficiency, increased fuel consumption, unusual noise, and frequent maintenance issues. Additionally, visual indicators like cracks, corrosion, or blade erosion often signal that it’s time for repairs.
Key Turbine Refurbishment Techniques
1. Blade Repair and Replacement
Turbine blades endure extreme operating conditions, including high temperatures, pressure fluctuations, and corrosive environments. Over time, these factors lead to wear, cracks, and material degradation, reducing turbine efficiency and increasing maintenance costs. Instead of costly replacements, advanced blade repair techniques offer a reliable and cost-effective way to restore performance and extend service life.
From precision welding and laser cladding to thermal spray coatings and 3D-printed repairs, modern repair solutions can restore damaged blades to near-original condition. These cutting-edge methods not only enhance durability but also improve turbine efficiency, reducing downtime and operational expenses.
2. Rotor and Stator Refurbishment
The rotor and stator are critical components that impact turbine efficiency. Refurbishment may involve rewinding, rebalancing, and recoating to enhance performance and prevent unplanned downtime.
3. Bearing and Seal Upgrades
Worn bearings and seals can lead to leaks and reduced efficiency. Upgrading to advanced materials and precision-engineered components enhances durability, reduces friction, and minimizes energy loss.
4. Advanced Coating and Surface Treatments
Protective coatings such as thermal barrier coatings (TBCs) and anti-corrosion treatments help improve turbine longevity by reducing wear and environmental damage.
5. Control System Modernization
Outdated control systems can limit performance and monitoring capabilities. Upgrading to digital control systems with real-time monitoring, predictive analytics, and automation can optimize turbine performance.
Innovative Technologies in Turbine Refurbishment
Use of AI and Predictive Maintenance
AI-driven predictive maintenance systems analyze performance data to identify potential issues before they cause failures, enabling proactive refurbishment.
3D Printing for Custom Components
Additive manufacturing allows for the creation of custom turbine components with high precision, reducing lead times and enhancing repair efficiency.
Laser Cladding for Surface Restoration
Laser cladding is a cutting-edge refurbishment technique that applies wear-resistant materials to turbine components, restoring their original specifications and extending their lifespan.
Cost-Benefit Analysis of Refurbishment vs. Replacement
When to Refurbish vs. When to Replace
Refurbishment is ideal when components can be restored at a lower cost than full replacement. However, if the turbine is outdated or heavily damaged, replacement may be the better option.
Long-Term Savings and ROI Considerations
Refurbishing turbines can extend their lifespan by several years, reducing capital expenditures and ensuring a higher return on investment compared to purchasing new equipment.
Managing Turbine Component Fatigue
Turbine components, such as blades, rotors, and seals, endure intense stress during operation, with constant exposure to high temperatures, pressure variations, and mechanical forces. Over time, these conditions can lead to component fatigue, a major cause of turbine failure. Fatigue occurs when materials are subjected to repeated stress, causing microscopic cracks that grow over time and can ultimately lead to catastrophic damage.
Effectively managing turbine component fatigue is essential for maximizing performance and extending the lifespan of turbines. Strategies like material selection, design optimization, advanced monitoring techniques, and regular inspections can help identify early signs of fatigue before they result in serious damage. Additionally, implementing refurbishment techniques such as welding, coating, and thermal treatments can restore the integrity of fatigued components and prevent failure.
WOC: Leading Supplier of New and Refurbished Gas Turbine Control System Parts
WOC is a leading supplier of both new and refurbished gas turbine control system parts, offering high-quality solutions for power plants and energy companies worldwide. With a commitment to providing reliable and cost-effective components, WOC ensures the smooth operation of gas turbine systems by offering a comprehensive range of parts, from advanced control modules to essential sensors and valves. Whether for immediate replacement needs or long-term maintenance projects, WOC’s products meet the highest industry standards, helping businesses maintain efficiency and minimize downtime. Their expert knowledge and dedication to customer service make them a trusted partner in the gas turbine industry.
IS200HFPAG2A, IS200SCTTG1A are examples of GE gas turbine control system parts.
Conclusion
Turbine refurbishment is a cost-effective way to enhance performance, extend lifespan, and reduce operational costs. By implementing advanced refurbishment techniques and leveraging modern technologies, industries can maximize efficiency and reliability. Staying ahead with regular maintenance and predictive strategies will ensure turbines continue operating at peak performance for years to come.
What's Your Reaction?

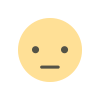

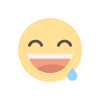


